What is Partial Discharge and why test for it?
Partial Discharge (PD) is an electrical discharge or spark across a void or gap. This can take place between two electrodes (e.g. in a motor, the copper conductor and earth) without completely bridging across the two electrodes — Hence the term “Partial”.
These voids and gaps occur because of
- manufacturing processes,
- thermal deterioration over time,
- poor fitting of the coils,
- and coil movement due to looseness and vibration etc.
Other forms of PD can also be found on surface of the windings due to conductive contamination or on the end windings between adjacent coils of different phases.
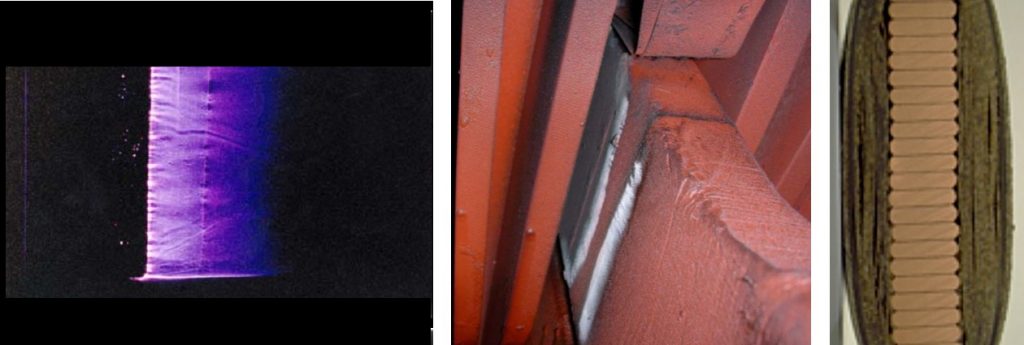
All high voltage motor windings will have some PD, even when new. This is due to the nature of the windings and the manufacturing methods required. As the insulation degrades the number and magnitude of the PD increases. The increase in PD causes further erosion of the insulation.
PD Testing is a very useful tool for evaluating the condition of high voltage machine windings from around 4kV and above. With repeat testing over appropriate time intervals the rate of deterioration can be observed. Although the actual time of failure cannot be predicted with 100% confidence, the information can be used to assess the risk of failure and appropriate contingencies, maintenance and repair actives planned accordingly.
How is Partial Discharge tested?
PD Testing can be carried out off-line using our state-of-the-art QLF kit and also on-line following installation into the machine of appropriate sensors such as Capacitive Couplers, Rogowski coils, RF CT’s etc. In addition to rotating machine windings, PD testing can also be used on Switch Gear, Transformers and Cables.
High Voltage testing at 50Hz/60Hz requires a large power source, often weighing several tonnes, with a large footprint. Due to the practical challenges associated with such a large power source, PPI Engineering use a more portable technology that incorporates a Very Low Frequency (VLF) power source at 0.1Hz. This enables us to transport equipment that can be wheeled around in a trolley case – allowing access to even the most inhospitable environments.
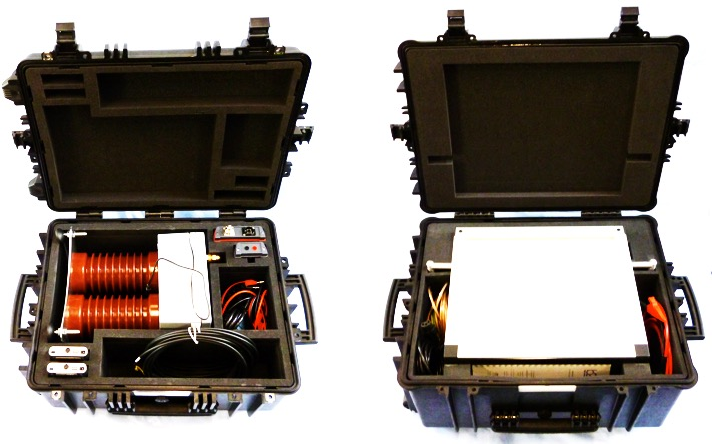
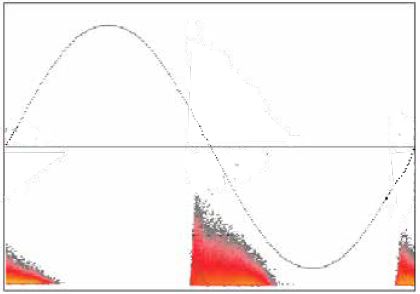
The PD measurements produce a pattern of scattered discharge points as displayed above. These patterns are plotted in various shapes and forms, depending on the location and severity of discharge. Our engineers have extensive experience in assessing these PD patterns to identify the area and severity of discharge in your stator winding. We can narrow down the root cause and recommend a corrective remedial action using this analytical method.
It is important that periodical measurements are also taken on healthy machines to form a trend. This can be logged to provide the end-user with a clearer picture of the windings’ condition over time, providing advance warning of any potential issue.